Imagine a manufacturing environment where humans and robots work hand in hand, seamlessly collaborating to achieve unprecedented levels of productivity, efficiency, and safety.
Now, ask yourself: Is this futuristic vision already becoming a reality?
Are cobots the groundbreaking innovation that will shape the future of the manufacturing industry?
The answer lies in exploring the remarkable world of cobots—collaborative robots designed to revolutionize the way we manufacture. The air is charged with excitement as cutting-edge technology unleashes a new era of productivity, safety, and innovation. It’s the world of cobots—collaborative robots—and they are poised to transform the manufacturing industry as we know it.
Can Cobots Ignite a Revolution in the Future of Manufacturing?
In this blog post, we invite you to buckle up and embark on an exhilarating journey into the future of manufacturing, where cobots are the superheroes revolutionizing the very fabric of the industry.
What are Cobots?
Cobots are robotic systems designed to collaborate and work alongside human operators in a shared workspace. Unlike traditional industrial robots that are typically isolated from humans, cobots are equipped with advanced sensors, vision systems, and algorithms, allowing them to interact and cooperate with humans effectively.
They can perform a wide range of tasks, from simple repetitive actions to complex assembly processes, making them versatile assets in the manufacturing environment.
Advantages of Cobots in Manufacturing
1. Increased Efficiency
Cobots automate repetitive and mundane tasks, allowing human workers to focus on more valuable and skilled work. By working in tandem with humans, cobots can significantly increase overall productivity, reduce cycle times, and enhance operational efficiency.
2. Improved Safety
Safety has always been a primary concern in manufacturing. Cobots are designed to work safely alongside humans, employing various sensors and safety features. They can detect and react to human presence, ensuring worker safety and reducing the risk of accidents.
Cobots have the potential to create a safer work environment by taking on hazardous tasks, such as lifting heavy objects or working in dangerous conditions.
3. Flexibility and Adaptability
Traditional industrial robots are often bulky and require dedicated infrastructure. In contrast, cobots are lightweight, portable, and easy to program. They can be quickly reconfigured to perform different tasks, making them highly flexible and adaptable to changing manufacturing needs.
This versatility enables businesses to streamline production processes and respond swiftly to market demands.
Enhanced Collaboration between Humans and Cobots
Cobots are not intended to replace human workers; instead, they are designed to work alongside them, complementing their skills and capabilities. The collaboration between humans and cobots brings forth a synergistic effect, where the strengths of both are combined.
Cobots can handle repetitive tasks with precision, while humans excel in decision-making, problem-solving, and creativity. This collaboration fosters innovation and creates opportunities for upskilling and reskilling the workforce.
Applications of Cobots in Manufacturing
1. Assembly and Inspection
Cobots excel in repetitive assembly tasks, ensuring consistent quality and accuracy. They can also perform inspection and quality control processes, identifying defects with precision.
2. Material Handling
Cobots can lift and move heavy objects, reducing the physical strain on human workers. They can work seamlessly alongside humans on assembly lines or in warehouse environments, optimizing logistics and minimizing downtime.
3. Machine Tending
Cobots can operate and tend to machines, such as CNC mills or injection molding machines, improving efficiency and freeing up human workers for more complex tasks.
4. Collaborative Welding
In welding operations, cobots can assist human welders by performing repetitive welding tasks, ensuring consistent weld quality, and minimizing the risk of exposure to hazardous fumes.
Challenges and Future Outlook
While cobots offer immense potential, their widespread adoption in manufacturing does face some challenges. These include initial investment costs, integration with existing systems, and the need for specialized training.
However, as technology advances and costs decrease, we can expect to see more and more companies embracing cobots as integral components of their manufacturing processes.
The future of cobots in manufacturing is bright. With advancements in artificial intelligence, machine learning, and robotics, cobots will become even more capable, intelligent, and efficient.
They will continue to revolutionize industries, making manufacturing safer, more productive, and adaptable to changing demands.
Cobots represent a remarkable leap in the evolution of manufacturing. By blending the strengths of humans and robots, they enhance efficiency, safety, and flexibility on the shop floor.
The era of cobots in manufacturing has only just begun, and the possibilities they bring are endless. Embracing this technology will not only pave the way for a more efficient future but also create new opportunities for innovation and growth within the manufacturing industry.
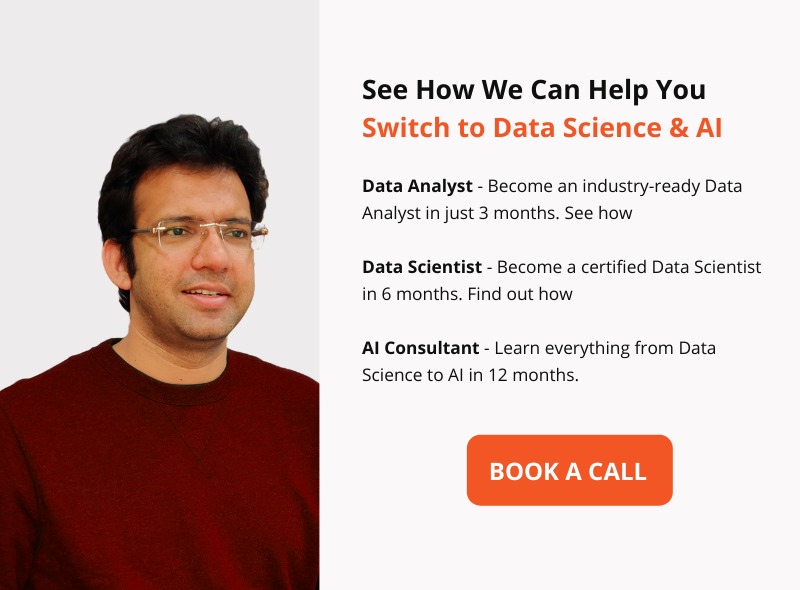
Stay curious, keep exploring, and get ready for the AI-driven world ahead!
Join ACCREDIAN’s Data Science certifications and start your journey today! With our extensive collection of data resources, pursue a fulfilling career in data science.
Let’s make your data-driven dreams a reality!
Contact us for any questions or comments.